The Canadian manufacturing industry has always had to adjust to big changes. During the Great Depression, manufacturers were forced to adapt to massive drops in demand and labor. In the 1980s, it was steel tariffs and subsidies that reshaped the competitive landscape. Then came trade liberalization in the 1990s, labor shortages in the 2000s, and global supply chain issues in more recent years.
Manufacturing has never stood still, and 2025 is no different. Some of the pressures today are new, such as the rapid pace of digital transformation and the growing demand for real-time data. Others will feel familiar to anyone who has spent time in this industry. Tariffs, talent gaps, rising costs, and uncertain global conditions are still very much in play.
One of the biggest shifts now is technology, particularly artificial intelligence (AI). It is being talked about as the next big thing in manufacturing. But here is the thing: most manufacturers are not using it. As of July 2024, only 3.7 percent of Canadian manufacturing companies have adopted AI. Many simply do not see how it fits into their day-to-day operations, or where to start.
Common Misconceptions About AI in Manufacturing
Part of the reason AI has seen slow adoption in manufacturing is down to misconceptions that make it seem riskier or less relevant than it really is. Here are three of the most common ones – and why they don’t hold up. “AI is just a trend.”
Trends typically follow a predictable pattern. They show a quick spike in interest, attract buzz, and then fade as reality sets in. 3D TVs got a lot of hype in the early 2010s, but when the reality of donning goggles and sitting perfectly still on your couch set in, the excitement wore off. That is not what we are seeing with AI in manufacturing. The global industrial AI market grew from $8 billion in 2019 to a projected $700 billion by 2032. That’s not hype. That’s momentum. And manufacturers who ignore it risk being left behind.
“AI is risky and unreliable.”
That might have rung true in 2001, but not today. AI has matured. While the technology continues to evolve, many of the tools being used in manufacturing, like predictive maintenance, quality control, and process monitoring, are already proven. They’ve been tested, refined, and deployed across thousands of real-world use cases. In fact, 61% of organizations say they can’t detect certain critical threats without AI. When implemented properly, it’s not experimental. It’s dependable. “AI will replace human jobs.”
AI can automate repetitive tasks, sure, but it doesn’t replace people. It supports them. It frees up time for decision-making, innovation, and solving real problems on the floor. Building the Right Foundation
To get there, you need the right foundation. In every factory that succeeds with AI, the same three pillars are always in place: people, processes, and technologies.
People drive progress. They are your operators, team leads, and experts. They bring years of hands-on knowledge that is not always written down but is critical to how things run.
When AI enters the picture, it can raise very real questions: What happens to my role? Will I be
replaced? Can I keep up? If those concerns are not addressed early, AI can lead to resistance, a sense of exclusion, and even a loss of expertise (if experienced workers choose to leave or disengage from the process). But when people are involved from the start and supported properly, it works. One manufacturer used AI to identify skill gaps, personalize training, and match people to roles more effectively. The impact was a 40 percent reduction in training time, a 35 percent increase in tech adoption, and better retention across the board.
Processes shape production. They might need to shift slightly to get the most out of new tools. That does not mean starting over—it means making smart adjustments that open the door for better performance.
Technology goes beyond machines—it’s how we innovate. It includes what you already have: ERP systems, MES platforms, sensors, dashboards. AI builds on these. But none of this works without direction. You need a clear vision, backed by strong intent. And that vision is not built all at once. It comes from small, well-orchestrated efforts that add up to lasting change.
Consider a Real-World Example: Reading Analog Gauges with AI
This kind of step-by-step thinking is exactly how one manufacturer approached a common challenge: pulling data from analog gauges and deriving insights from that data to make more informed decisions.
Analog gauges are still found on many factory floors. They measure critical values like pressure, temperature, and voltage, and they do the job well. However, because they were built for manual reading, not digital integration, collecting data from them at scale is difficult. Manually checking them takes time and can lead to errors.
The common fix is to replace them with newer, connected sensors, but that can be expensive. And in many cases, the gauges themselves still work just fine.
Instead of replacing the equipment, the team used AI and computer vision. They trained a model using both real and synthetic images to read different dial positions. With a simple camera setup and on-site processing, they were able to collect accurate, continuous readings automatically. This gave them better visibility into operations, helped with compliance and maintenance, and made it easier to spot issues early. All without changing the hardware.
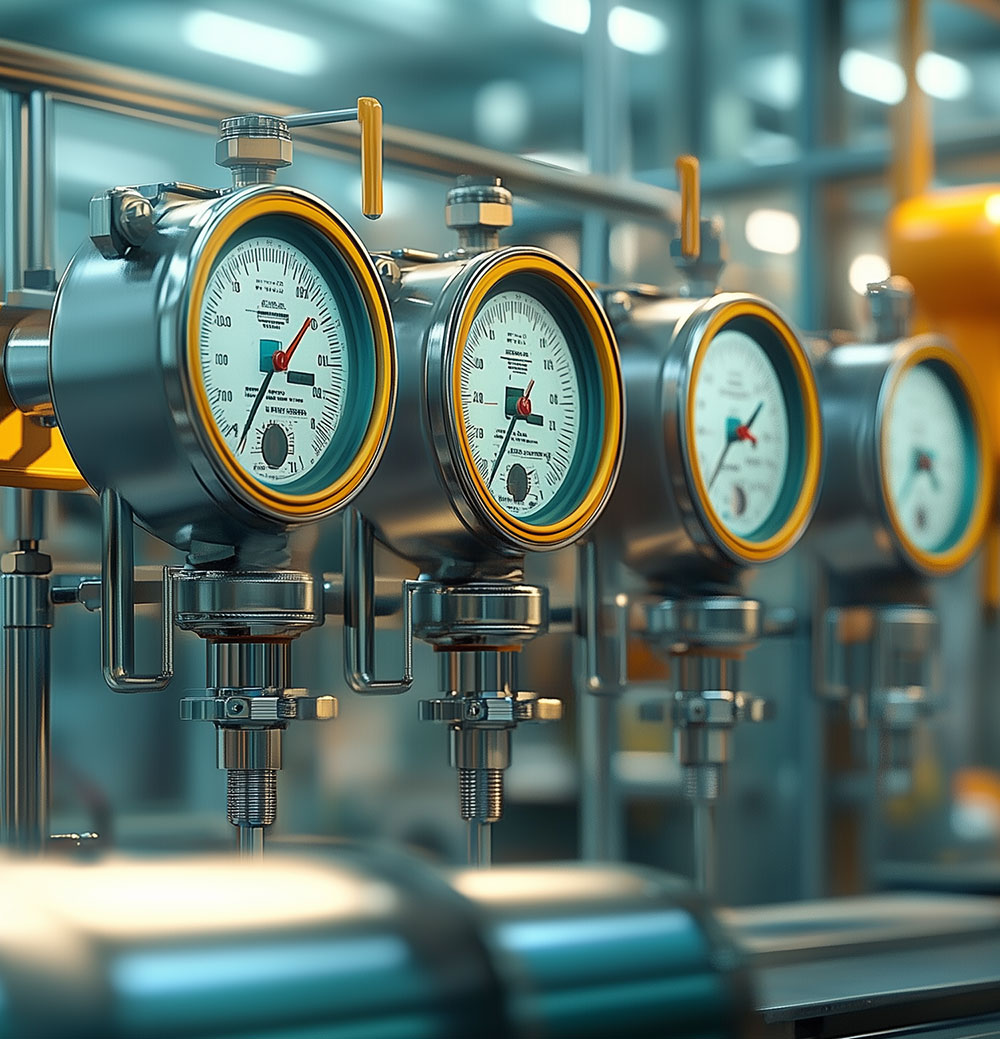
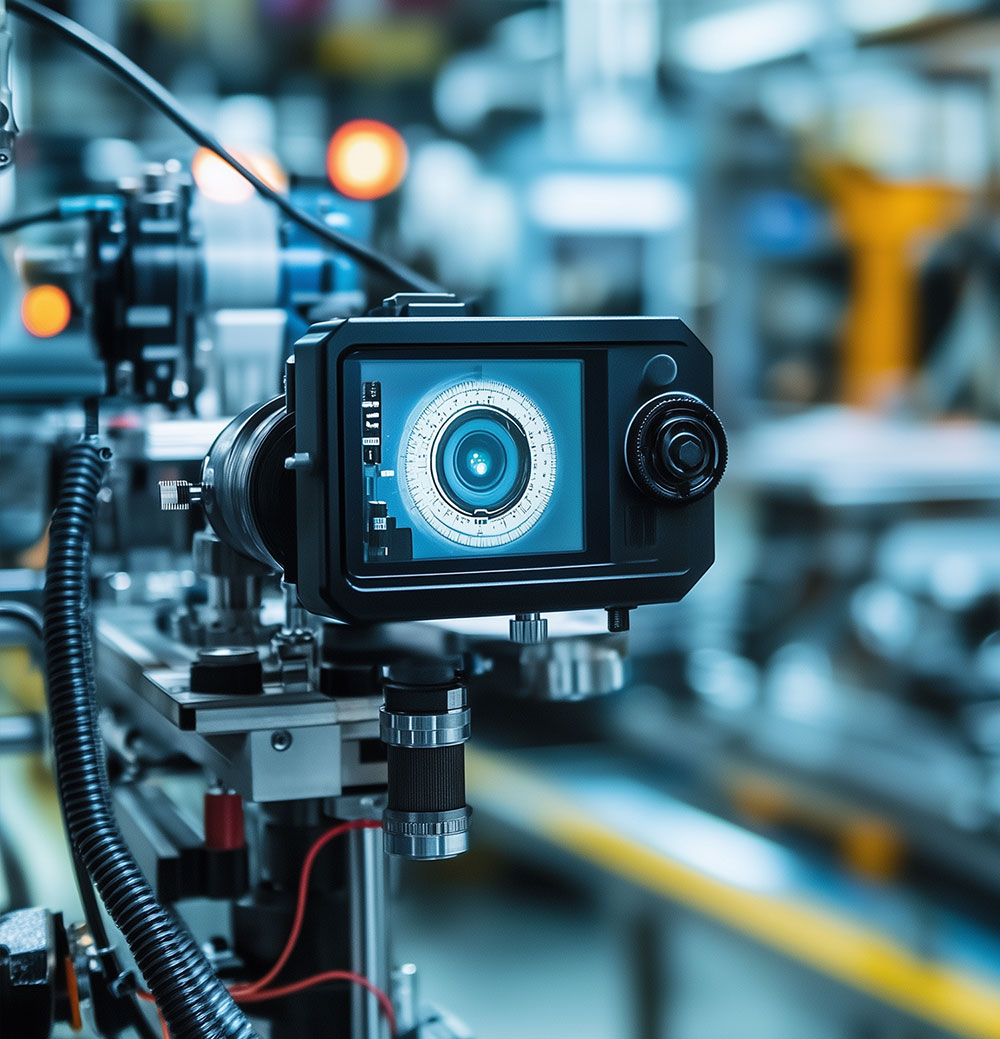
How AI Helps Prevent Downtime
The analog gauge example shows how AI can solve a specific problem. But we can apply the same focused and practical approach across the entire production line.
Downtime is still one of the most expensive and disruptive issues in manufacturing. But if we use AI to improve how teams collect, interpret, and act on data, then we can help them spot issues earlier, respond faster, and plan maintenance more effectively. All of this translates to less downtime, lower costs, and better performance on the floor.
The impact is measurable. In production environments, we’ve seen:
- Up to 50 percent fewer breakdowns
- 25 percent lower maintenance costs
- 20 percent longer equipment lifespan
Manufacturers today are under intense pressure to improve reliability without increasing costs. Results like these can make all the difference between falling behind and staying competitive.
Think Big. Start Small. Move Fast.
You don’t need a complete plan to get started. The most impactful AI journeys begin by solving one specific, measurable problem. Run a quick diagnostic, identify a high-value use case, and take that first step. From there, you can scale with purpose and direction. And, in parallel you can build your longer-term strategic plan.
At KPI Digital, this is our approach to AI. We focus on the critical parts of your business, simplify the complex, and deliver real results. Ready to explore what AI can do for your organization? Contact us!
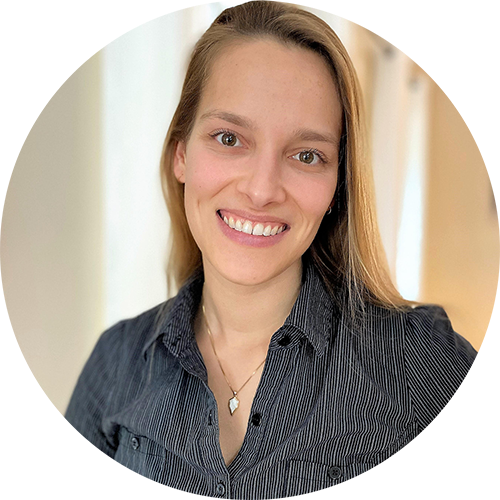
Jessy-Kate Fournier
Jessy-Kate, Solution Architect and Pre-Sales Director at KPI Digital, specializes in Data Architecture, BI, AI, and Advanced Analytics. She drives innovation and data-driven transformation across North America, leading projects in Manufacturing, Supply Chain, Sales, and Marketing to deliver measurable business results.
Connect with Jessy-Kate on LinkedIn

Bryan Minor
Bryan, an AI expert with 30 years of experience, has developed advanced solutions for the defense, biotech, and advertising sectors. A specialist in numerical optimization and computer vision, he combines innovation, business acumen, and deep expertise in AI development. He holds a Top Secret/SCI clearance from the U.S. Department of Defense.
Connect with Bryan on LinkedIn